GBG Mannheim is tackling defects with easysquare – mobile recording for acceptance, documentation and defect monitoring in construction project management
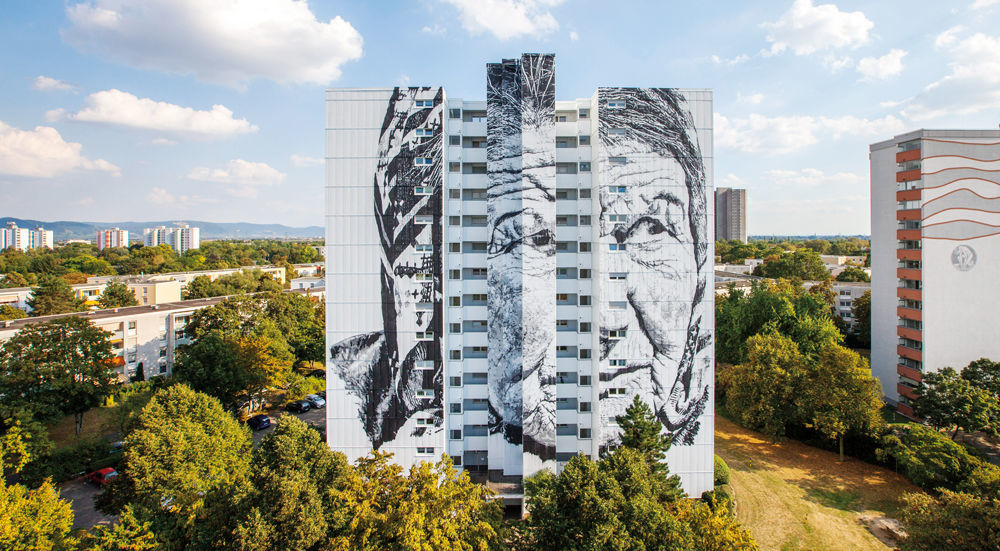
Calculations like this are so simple that most of us do not even give them a second thought. Companies often face the same kinds of questions, and come to similar conclusions: to use proven solutions of known quality rather than taking the significant risk of trying to integrate stand-alone solutions into existing system landscapes.
The easysquare approach – a solution for all cases
GBG Mannheim, the region of Baden-Württemberg’s largest municipal housing association with approximately 19,000 apartments, has been using various easysquare mobile services for several years now. This enables mobile recording of apartment handovers, vacant apartment inspections and quality controls, all via an app. In 2018, GBG Mannheim decided to digitise yet another previously paper-based process. The goal was to free acceptances and inspections of real estate objects in new construction and modernisation projects from the usual flood of paper. The fruitful collaboration with GBG Mannheim over the last few years and their success with our previously implemented solutions made working with PROMOS on this next step a no-brainer. Klaus Lange, project manager for GBG Mannheim, explains the special focus of the project: “Our aim was to not only offer the internal project managers, architects and site managers a mobile solution, but to embed this function in the existing SAP® landscape in the best way possible.”
Keeping an eye on defects – mobile and on site
The resulting solution is designed in such a way that the responsible employee receives a corresponding digital form in their easysquare mobile work basket upon initiation of an inspection or acceptance in SAP® for a certain new construction or modernisation project. The header data for the project has already been entered here. Real estate data, the SAP® project number and the names of project and site managers are fed directly from master data in the GBG Mannheim SAP® system. Things can get going right away. The employee first has the opportunity to enter a short written assessment of the general status of the project. This is aided by a pre-defined electronic checklist, which they can use to orient themselves and record the construction progress. All defects identified must be documented with utmost precision in an acceptance or inspection. The employee is aided here by an already saved object structure added to the project from the technical location structure. The selection catalogue already presents the employee with suggested trades based on the area selected in the app. For instance, a plumbing defect cannot be recorded in a building’s hallway. The employee precisely identifies the defective work using the catalogue structure. They can then attach a photo and add pointers for clarity. The employee entering the data can also select from various criteria, such as whether the defect is critical, open, requires subsequent acceptance or entails a rent reduction. Every recorded defect receives an individual ID in SAP® to ensure clear assignability. Since the individual trades are linked with the relevant suppliers in the system, an e-mail requesting defect rectification can be sent directly from the app with the appropriate deadline. GBG Mannheim has the flexibility to adjust the selectable options as needed at any time. Once the acceptance or inspection is completed, the recorded data is fed back into the GBG Mannheim SAP® system.
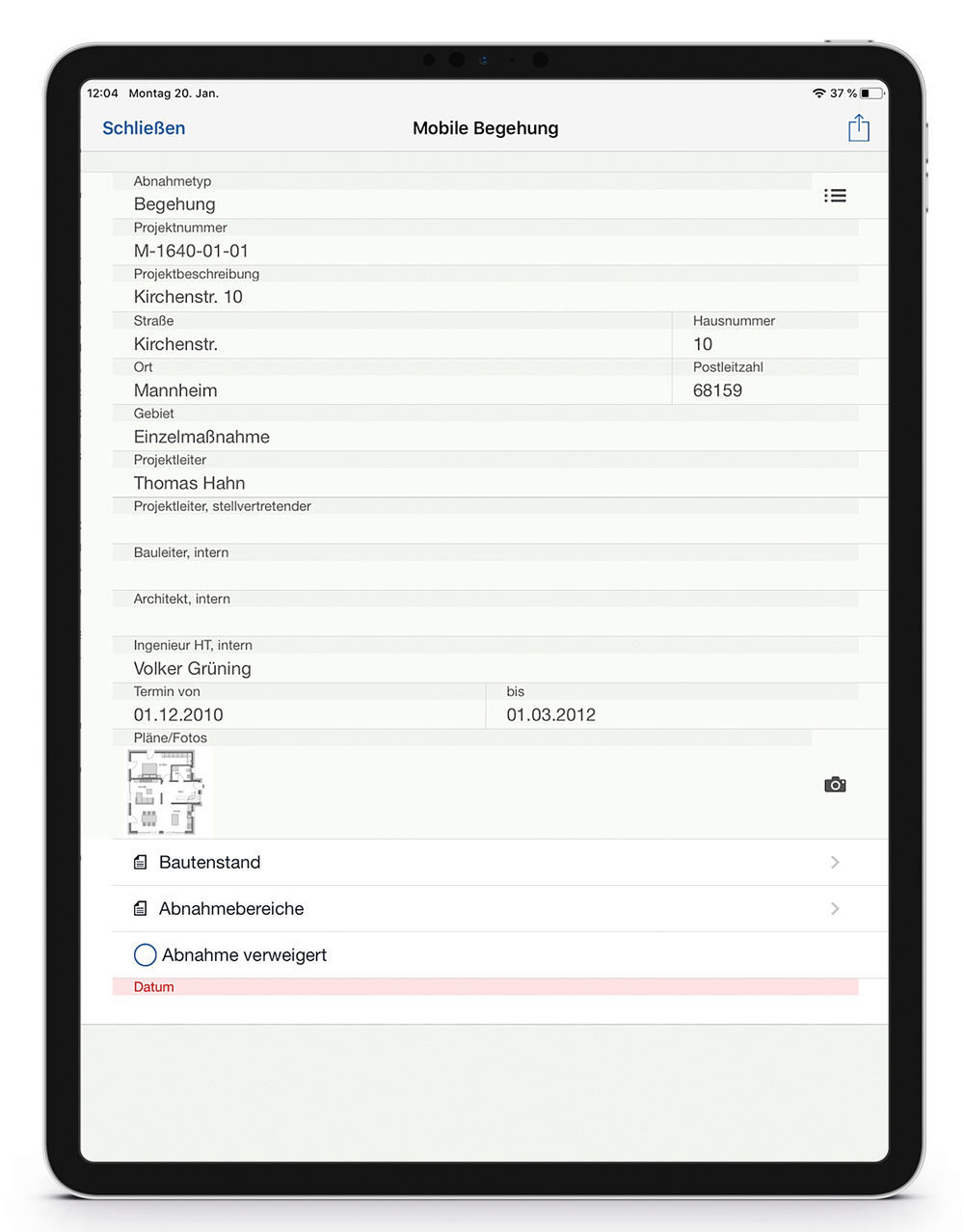
Figure 1: Data from the SAP® system of GBG Mannheim has automatically been entered into the form for planned inspections of new construction and modernisation projects.
Everything in one box – the defect cockpit for easy monitoring in SAP®
The data fed back into the system is both added to the relevant project in the form of a log in SAP® and saved in the SAP® defect cockpit. A traffic light function provides a clear overview of all recorded defects and their respective status. The project manager can easily track which defects are open and which ones have been rectified. A filter function makes for easy sorting by site manager, project or supplier. The defect report for the supplier can also be generated directly in the cockpit. “With the defect cockpit, construction managers now have a unique tool that provides full transparency regarding existing defects. It also allows them to press ahead with defect rectification in a particularly quick, effective and documented manner,” Lange explains.
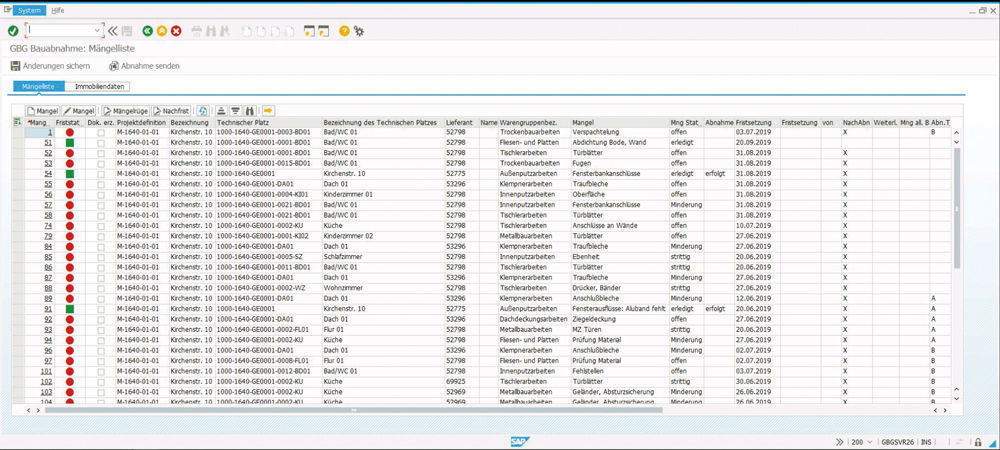
Figure 2: The status of existing defects is clearly shown in the defect cockpit with a traffic light function.
Trust is good, control is better – additional site inspections made easy
A project manager’s work is by no means complete with the identification and reporting of a defect. An especially important step is the subsequent additional inspection, which is why this can be initiated directly from the defect cockpit. This involves checking whether the relevant supplier has begun rectifying the defect or whether a reminder or warning must be sent. Follow-up inspections also serve to determine whether the defect has been repaired to the full satisfaction of the client. To do this, the agent again navigates in the easysquare app to the area of the building in which the defect was identified. An icon indicates that data has been recorded here. The respective employee can call up all details recorded on the defect and subsequently decide whether it has been successfully rectified. Should this be case, they can mark the defect as completed in the app. The defect will then no longer appear in the next inspection. If the defect is still present, the next step in the escalation chain can be activated. On the legal basis of the VOB (German Construction Tendering and Contract Regulations), notifications of defects are generated with the relevant project and contract data and sent on the relevant deadlines.
Always available – ad-hoc inspections with real-time data
Not every inspection of new construction and modernisation projects is planned in advance. Some situations call for a spontaneous inspection of construction progress. The easysquare app also contains empty forms to document any defects or the general condition of the building in such cases. Upon selection of an active new construction or modernisation project, the form is filled in real time with the necessary data from the company’s SAP® system. Ad-hoc inspections can thus be easily conducted at any time – without the need to manually enter the results in the SAP® system later.
Klaus Lange, project manager, GBG Mannheim
A successful project with further potential
Defect management has already been in operation at GBG Mannheim since December 2019. Since then, the relevant employees have gradually been switching to inspections via the easysquare app – a total of 20 users. Lange is very pleased with the successful implementation of the project. “The new solution connects two worlds for us in the most ideal way: both the real world in which the construction or modernisation project is tangibly executed and the SAP® world in which we store all the relevant data and control the project. This highly integrated, seamless process grants us significantly higher data quality. Furthermore, we anticipate that the holistic approach will lead to quicker, more consistent defect monitoring over time.” The project is to be followed by further collaboration with PROMOS to implement even more improvements. The defect follow-up is to be connected to the warranty tool in SAP®, for example, and there are plans for mobile construction site documentation, which will send images to a photo database in Microsoft® SharePoint. Also planned is the recording of correspondence activity such as reminders, terminations and final acceptance sent to suppliers.
Author:
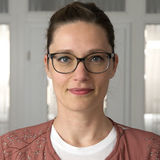
Kathrin Finn
Head of Product Management
PROMOS consult
Other articles by this author:
- Article "Mobile project management – efficiently manage internal pipe rehabilitation projects and orders"
- Article "Practical and efficient – The new functions of the craftsmen portal"
- Article "GBG Mannheim is tackling defects with easysquare – mobile recording for acceptance, documentation and defect monitoring in construction project management"