KoWo is settling up! Automated posting of apportionable services in the craftsmen portal
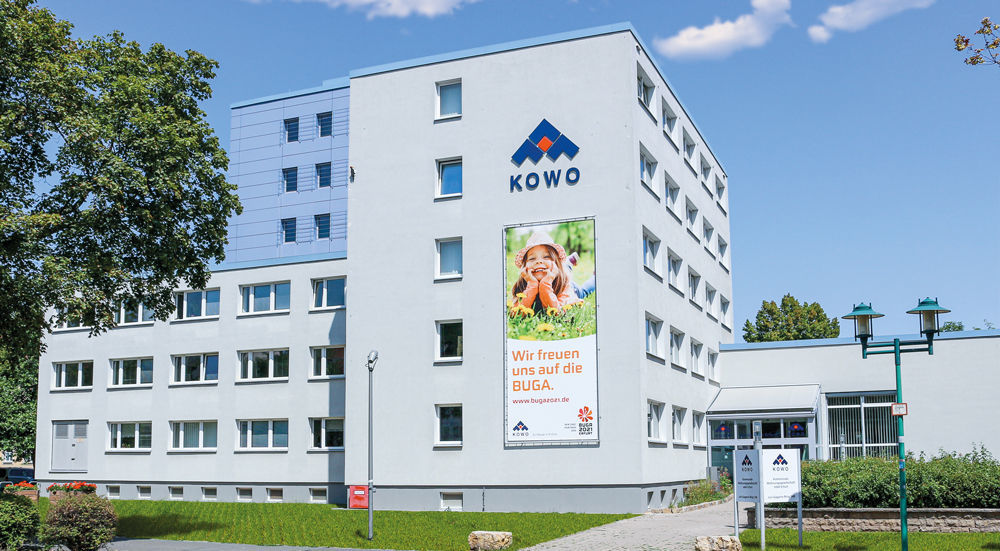
The long path of maintenance billing
Before KoWo decided to completely change direction in its accounting of apportionable operating costs, the booking of apportionable invoices often required multiple loops through the company. The contractors were commissioned via fax, e-mail or telephone, and the relevant bill for the completed service arrived – sooner or later – at KoWo by post. But the real work was only just beginning: a consignment slip would be printed and added to the invoice before it was finally sent on to the ordering party. This person would then have to decide which, if any, services were apportionable and which settlement unit (SU) to book them to. Can the costs be assigned to one building, for example, or were services provided across multiple accounting entities (AE), as with courtyard cleaning conducted on two neighbouring AEs? With a wide range of service providers and so many orders, this entailed enormous manual effort.
Hurdles seldom appear alone
“Since we were already using SAP® and the PROMOS craftsmen portal for the performance and mapping of our maintenance orders, it was an obvious choice to also use these systems for apportionable operating costs”, said Uta Henze, project manager for operating costs, of KoWo’s strategic thinking. But where exactly were the barriers that had prevented such a project from getting off the ground? These were chiefly technical in nature. While the costs for maintenance services were previously posted to the relevant orders, it was now necessary to ensure that they could be assigned to the respective settlement units in the most automated way possible. To achieve this, it was necessary to expand the relevant data structures in SAP® (functional locations and modules), maintain the relevant assignment tables and save the maintenance plans in the system. Furthermore, it was necessary to ensure that employees in the operating costs department have data sovereignty regarding the posting of costs. When the project started in October 2018, KoWo selected a small interdisciplinary team with one member from each of the sales, IT and operating costs departments.
Uta Henze, project manager for operating costs, Kommunale Wohnungsgesellschaft mbH Erfurt
Desired results through solution optimisation
The outcome of the technical optimisations undertaken over the course of the project differentiates between two separate courses of action. Recurring work conducted at regular intervals with a fixed date (e.g. apportionable cleaning services) is planned automatically through maintenance plans stored in SAP®. Orders that occur more spontaneously, such as bulky waste removal, are entered manually by an employee via the OPSN screen. Once the operating company has entered the service in the craftsmen portal, the service entry sheet is imported into SAP® and can then be released. The contractor automatically receives a credit note from KoWo. The SAP® system automatically assigns the costs to a settlement unit based on a saved customising table. It is even possible to automatically split apportionable and non-apportionable costs and to differentiate between material and wage costs. KoWo employees can then initiate the new transfer posting report introduced by PROMOS, which transfers the costs along with the proof of performance and credit note documents (Figure 1).
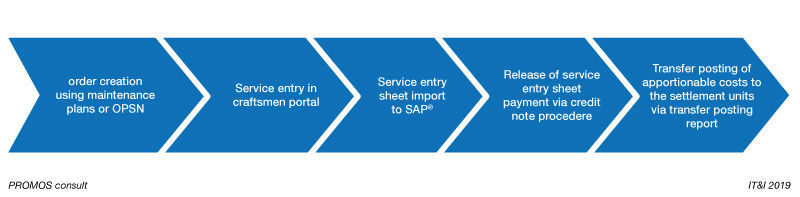
Figure 1: Since introduction of the new solution at KoWo, apportionable costs are posted automatically and systematically.
![]() Figure 1: Since introduction of the new solution at KoWo, apportionable costs are posted automatically and systematically. |
“The advantage of this downstream approach is that our operating costs team maintains full control over the relevant transfers. A traffic light system notifies them when certain constellations are not maintained in the Customising tables, for example, if a cost collector has not been generated or if a settlement unit does not yet exist. It is exactly the solution that we have been looking for”, Henze said. Among the wide range of optimisations is the uploading of KoWo’s existing maintenance plans from Excel into SAP®. They can now be edited en masse, for example, in the case of a minimum wage increase in the cleaning sector. Furthermore, the optimised display in the craftsmen portal now shows orders generated from maintenance plans separately from ad hoc orders (Figure 2). This measure prevents individual orders from getting lost within the sometimes long lists of automatically generated maintenance orders. Last but not least, KoWo employees can now use a report to automatically generate the customising tables that serve to assign orders, functional location and settlement units, or maintain these tables simply and conveniently themselves.
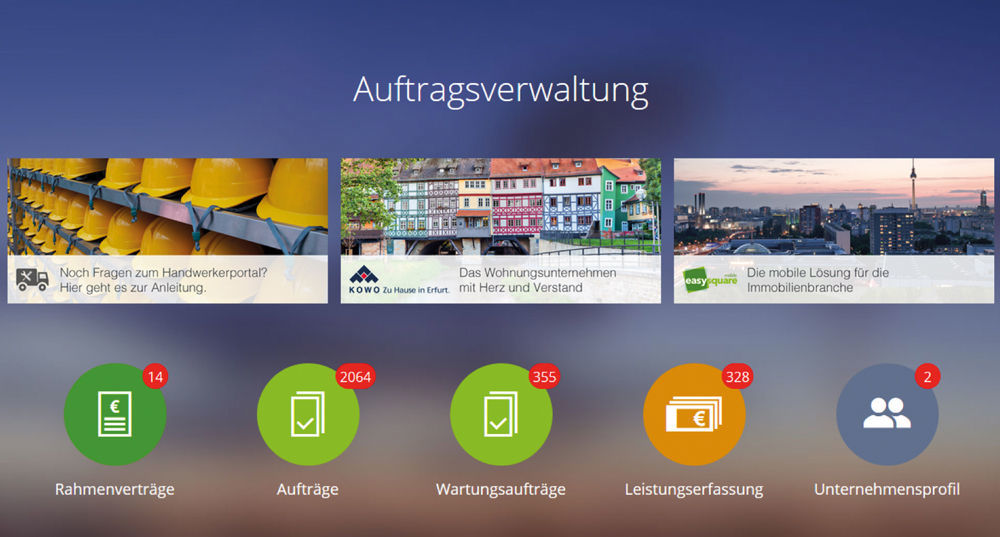
Figure 2: Ad hoc orders and those generated from maintenance plans are presented separately in the easysquare craftsmen portal for improved clarity.
Racing into the future
The completed project has successfully implemented a solution that allows KoWo to automatically settle its apportionable costs with system support. KoWo currently deploys the solution for planned house cleaning and irregular bulky waste removal appointments. The company plans to gradually expand the system to settle other operating costs as well, maintenance services in particular. “Today, we are already seeing an enormous increase in efficiency, not to mention the newfound transparency regarding costs, orders and statuses. We have significantly reduced our mountain of paper invoices. And no longer have to ask ourselves if an invoice has already arrived for service x. This happens automatically via the credit note procedure in the craftsmen portal. An absolute win-win situation for both sides”, said Henze of the new solution’s advantages. KoWo is planning a link to the easysquare public safety solution in the future. This will allow safety-relevant maintenance work to be mapped in the company’s safety precaution module. KoWo will be continually reducing its manual effort through planned optimisations and those that have already been implemented, leaving more time for what is really important.
Author:
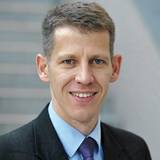
Eric Hoedke
Expert Consultant
PROMOS consult
Other articles by this author:
- Article "Well-informed – the new mobile report history for the easysquare professional app"
- Article "Fine tuning in purchasing – VW Immobilien is optimising the planning of their supplier orders with value contracts in SAP®"
- Article "KoWo is settling up! Automated posting of apportionable services in the craftsmen portal"
- Article "The new craftsmen portal – a modern look, high-speed performance and practical functions"
- Article "Rethinking claims processing"